ERP and PLM
What is ERP?
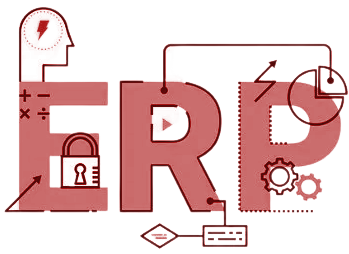
Enterprise Resource Planning (ERP) A business system used for Financial Management and reporting About the activity such as accounting, sales forecasting, production planning and execution, customer care and support, and transportation logistics Is.
The extent to which a company needs an ERP system to manage its finances often depends on the company's participation in it Process Production depends. Companies that have in-house manufacturing or complex engineering production to order products usually from one System They use comprehensive ERP to help organize information between their finance, sales and production departments.
Companies that outsourcing produce, often from a smaller suite of ERP tools that include financials, accounts payable, Accounts receivable, inventory and procurement modules use without the production resource planning module, hence References They are typically managed by outsourcing partners.
ERP systems enable organizations to plan for organization and profitability, by providing a real-time picture of Condition They make money to producers. With an ERP system in place, companies can track orders through receipts production and Track deliveries to gain a better understanding of inventory levels, delivery times, and production bottlenecks.
There are different types of ERP business systems in the market today with different features and features that are all in Serve to provide CFO They are available with detailed financial reports and insight into the financial future of a company.
What is PLM?
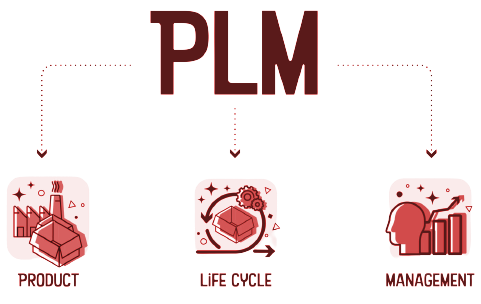
Product Lifecycle Management (PLM) It is a business system that controls product registration in all stages of development, from concept to design to provide production. With a PLM system in place, a company can product information including: bill of raw materials (BOM) , manufacturer approval lists (AML) and manage product documentation. The PLM system also allows a company to track each Enables changes in product information and communication between revisions to the supply chain.
With automated change processes built into PLM, companies can make key product decisions such as product changes in Manage real time. Perform engineering change requests and orders through a PLM system to integrating , Organize and track product information in a centralized location that would otherwise be spread across a wide range of organizational departments It was scattered throughout the company, it helps.
By capturing product information in a PLM system, manufacturers have an exclusive and correct version of their product registration at any point Access time and effective structure can simplify a change process.